В настоящее время зубчатые колеса нарезают в основном двумя методами: методом копирования и методом обката или огибания.
Метод копирования. Для нарезания зубчатых колес этим методом применяют инструмент, режущие кромки которого имеют очертание, соответствующее контуру впадины нарезаемого зубчатого колеса. В качестве такого инструмента используют модульные фрезы (дисковые или концевые) (рис. 1, а, б, в) или же фасонные резцы. Обработка производится либо одним инструментом (поочерёдно каждую впадину), либо несколькими одновременно по числу впадин. Недостатки метода копирования: 1 – для обработки каждого зубчатого колеса с определенным числом зубьев и модулем требуется инструмент специального профиля, поскольку профиль зависит от модуля. смещения исходного контура и числа зубьев. 2 – точность нарезания зубчатых колес невысока, так как помимо погрешности, обусловленной неточностью работы делительного механизма, неизбежны погрешности, вследствие неточности инструмента. В связи с указанными недостатками к такому методу зубонарезания прибегают лишь при отсутствии зуборезных станков, а также для предварительного нарезания впадин (при черновой операции). При нарезании зубьев одним инструментом производится поворот головки на шаг зубьев, т.е. на 1/z часть оборота, где z – число зубьев нарезаемого колеса. Производительность при этом способе низка, так как зубья нарезаются каждый отдельно и требуют время на возврат инструмента в исходное
При этом методе инструментом служит фасонная фреза, профиль которой представляет копию впадины между зубьями колеса (рис. 1). Обычно для зубчатых колес применяют модульные дисковые фрезы, а для особенно больших зубчатых колес – фасонные пальцевые фрезы (рис. 1, в). С увеличением числа зубьев кривые эвольвенты зуба изменяются и приближаются к прямой линии, а при колесе с бесконечно большим количеством зубьев – рейке; эвольвента превращается в прямую линию (рис. 2). При точном нарезании колес с числом зубев от 12 до 300 одного модуля необходимо 288 фрез с различным профилем их зубьев. Такое количество фрез для колес только одного модуля иметь дорого и трудно, поэтому в зависимости от точности нарезания ограничиваются комплектом из 3,8,15 или 26 фрез вместо 288.
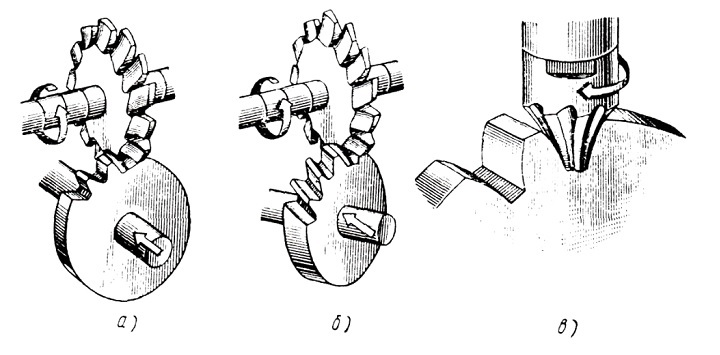
Рис. 1. Схема нарезания зубчатых колес методом копирования:
а – дисковой модульной фрезой цилиндрического колеса с прямыми зубьями; б – дисковой модульной фрезой цилиндрического колеса с винтовыми зубьями; в – пальцевой модульной фрезой цилиндрического колеса с прямыми зубьями
Каждая фреза из комплекта имеет свой номер и предназначена для нарезания колес с определенным диапазоном их зубьев. При комплекте из восьми фрез точно по профилю могут быть нарезаны колеса, имеющие число зубьев 12, 14, 17, 21, 26, 35, 55 и 135, а все остальные колеса получаются при нарезании неточного профиля.
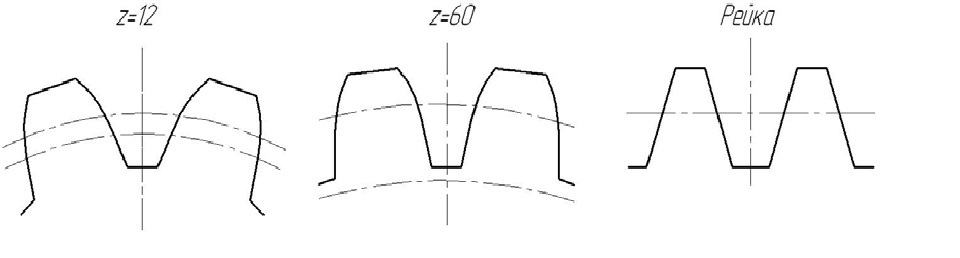
Рис. 2. Изменение профиля зубьев колес при увеличении зубьев
Увеличение количества фрез в наборе для более крупных модулей вызвано тем, что неточность нарезания одной фрезы колес с разными числами зубьев для больших модулей сказывается больше. По этой причине для точных колес более крупных модулей (свыше 16 мм) применяют комплекты, состоящие из 26 номеров фрез для каждого модуля. Подбор модульной фрезы для нарезания косозубых шестерен несколько сложнее, так как в этом случае необходимо учесть величину угла β наклона зубцов. Если для нарезания, например 32 косых зубцов модуля 6, взять фрезу №5 из 8-штучного набора, то это будет ошибкой, и в работе получится брак. В этом случае профрезерованная впадина между зубцами получится значительно шире, чем это требуется. Для того, чтобы получить правильный профиль у косых зубцов, необходимо модульную фрезу подбирать не по действительному числу зубцов, а по фиктивному. Это фиктивное число зубцов необходимо определять по следующей формуле:
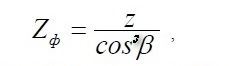
где Zф – фиктивное число зубцов фрезы, z – действительное число зубцов, β – угол наклона зуба.
Основная ошибка в профиле нарезаемого колеса здесь обусловлена тем, что косозубое колесо имеет эвольвентный профиль только в торцовом сечении, тогда как эвольвентный профиль фрезы располагается в сечении нормальном к направлению зуба.
Метод обката. При методе обката (огибания) заготовка и зубонарезной инструмент воспроизводят движения пары сопряженных элементов зубчатой или червячной передачи. Для этого инструменту придается форма зубчатого колеса, зубчатой рейки или червяка. Эвольвентную кривую АВ зуба, опишет точка А, принадлежащая прямой СС (рис. 3, а), если эту прямую перекатывать без скольжения по неподвижной окружности F. Отрезок DE, будет касаться эвольвентной кривой во всех положениях прямой СС. Это означает, что эвольвентная кривая в данном случае будет огибающей ряда последовательных положений отрезка DE, перемещающегося вместе с прямой АС.
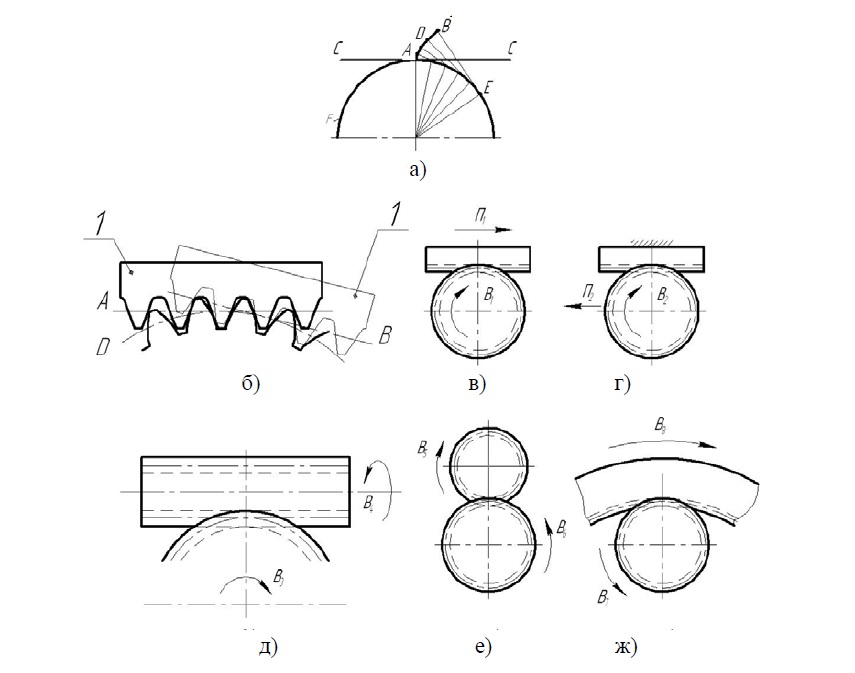
Рис. 3. Схемы зубонарезания методом обкатки
Для образования профиля зуба цилиндрических колес методом обката исходной рейке 1 с прямолинейным производящим контуром АВ (рис. 3, б) сообщают движение качения относительно нарезаемой заготовки (по делительной окружности Д). Образуемый таким способом профиль зуба является огибающей положений производящего контура. Это исполнительное движение формообразования профиля зуба является сложным и осуществляется в станках двумя элементарными взаимосвязанными движениями. Возможны схемы нарезки зубьев при движениях П1 и В1 (рис. 3, в) или при движениях П2 и В2 (рис. 3, г). Вариант относительного движения гребенки при неподвижной заготовке в практике не используется, так как в этом случае усложняется конструкция станка. Если рейки размещены на цилиндре так, что производящие контуры располагаются по винтовой линии, то режущая рейка становится червячной фрезой, и исполнительное движение формообразования состоит из двух вращательных движений В3 и В4 (рис. 3, д). В качестве производящего контура, кроме зуба рейки, можно использовать также зубчатые цилиндрические колеса. Тогда исполнительное движение образуется из двух взаимосвязанных вращательных движений В5 и В6 (рис. 3, е) при нарезании колес с внешним зацеплением и В7, В8 при нарезании колес с внутренним зацеплением (рис. 3, ж).